Interested in learning more about our Dew Point Sensor and pricing ? Contact us today to speak with one of our experts and get all the information you need to make an informed decision. Don't miss out on this opportunity to optimize your operations with the most accurate and reliable dew point measurement technology. Contact us now!
Dew Point Sensor - HENGKO® HT608
Industrial Dew Point Sensors for Environmental Temperature and Humidity Monitoring
The compact HT-608 Dew Point Transmitter with a measuring range down to -60 °C (-76 °F) Td and
outstanding price/performance ratio is dedicated for applications in compressed air systems,
plastic dryers and industrial drying processes.
* Dew point sensor for compressed air
* Output Modbus/RTU
* NEW Weatherproof, dustproof, and water-resistant—IP65-rated enclosure
* Fast response precision sensors provide accurate, repeatable readings
* Dew Point Sensor / Transmitter for Industrial Drying Processes
* -60°C OEM dew point sensor
* High pressure option for 8KG
Features
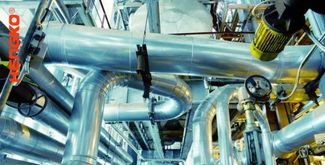
Specifications
Type |
Technical Specifications |
|
Current |
DC 4.5V~12V |
|
Power |
<0.1W |
|
Measurement range
|
-20~80°C,0~100%RH |
|
Pressure |
≤8kg |
|
Accuracy |
Temperature |
±0.1℃ ( 20-60℃ ) |
Humidity |
±1.5%RH(0%RH~80%RH,25℃ )
|
|
Long-term stability |
humidity:<1% RH/Y temperature:<0.1℃/Y |
|
Dew point range: |
-60℃~60℃(-76 ~ 140°F) |
|
Response time |
10S ( wind speed 1m/s ) |
|
Communication interface |
RS485 / MODBUS-RTU |
|
Records and Software |
65,000 records, with Smart Logger professional data management and analysis software |
|
Communication band rate |
1200, 2400, 4800, 9600, 19200, 115200(can be set), 9600pbs default |
|
Byte format
|
8 data bits, 1 stop bit, no calibration
|
Models
Step 1: Choose Models
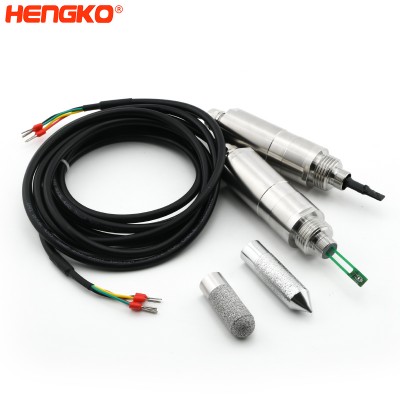
HT-608A (STANDARD)
Basic G 1/2"
This economical, compact dew point sensor is suitable for refrigerant, desiccant, and membrane dryers.
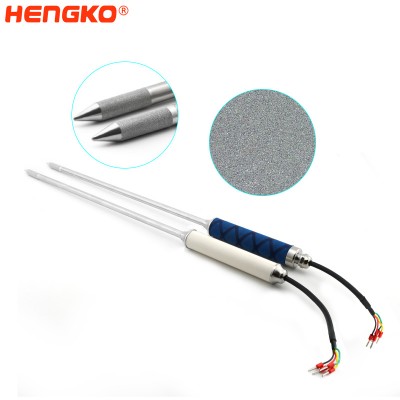
HT-608 C
Extra Small Diameter
Measurements in small holes and narrow passages.
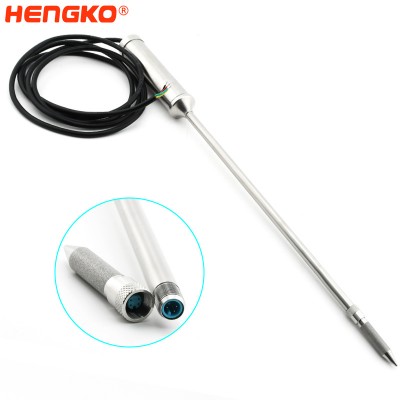
HT-608 D
Pluggable and exchangeable
An ideal everyday spot-checking tool. It is compact, portable, and provides reliable measurements in a wide range of applications.
Click model to download cutsheet
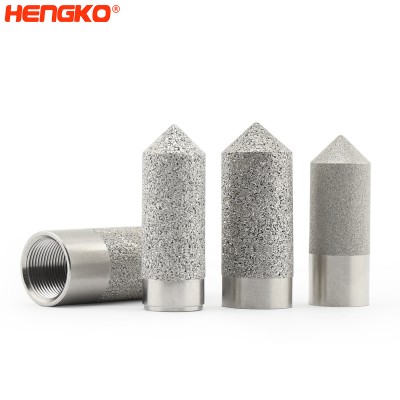
Pointed
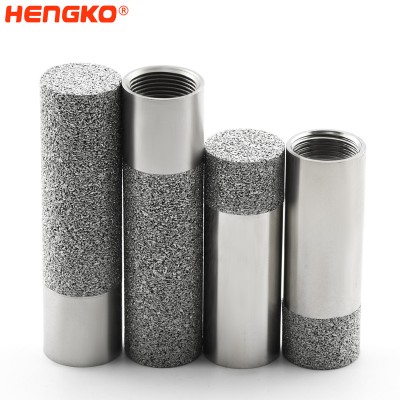
Flat top
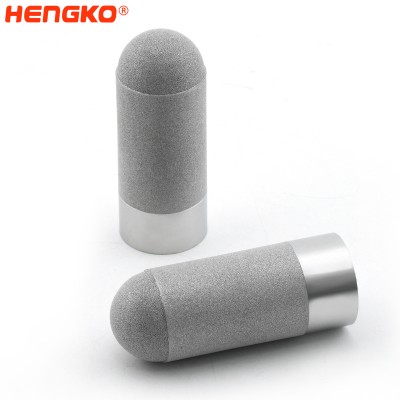
Dome
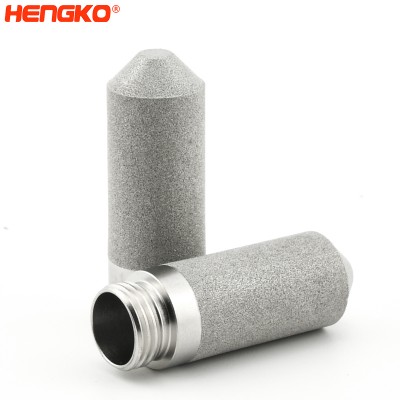
Conical
Applications
Dew point sensors and transmitters are used in a variety of applications to monitor the dew point of gases and liquids.
The dew point is the temperature at which water vapor in the gas or liquid will condense into liquid water.
By monitoring the dew point, it is possible to ensure that the gas or liquid is dry enough for safe operation and to prevent condensation.
Dew point sensors and transmitters are available in a variety of configurations to meet the needs of different applications.
Some of the factors to consider when selecting a dew point sensor or transmitter include the type of gas or liquid to be monitored,
the desired accuracy, and the environmental conditions.
* Compressed Air Drying:
Dew point sensors are used to monitor the dew point of compressed air to ensure that it is dry enough for use in critical applications.
* Refrigeration:
Dew point sensors are used to monitor the dew point of refrigerants to ensure that they are dry enough for use in refrigeration systems.
* Humidity Control:
Dew point sensors are used to monitor the dew point of air to control humidity levels in a variety of applications, such as food processing and pharmaceutical manufacturing.
* Building Automation:
Dew point transmitters are used in building automation systems to monitor the dew point of air in buildings to control humidity levels and prevent condensation.
* Process Control:
Dew point transmitters are used in process control systems to monitor the dew point of gases in industrial processes to ensure that they are dry enough for safe operation.
* Environmental Monitoring:
Dew point transmitters are used in environmental monitoring applications to monitor the dew point of air to track changes in humidity and identify potential problems, such as mold growth.
As you know, Dew point sensors and transmitters are an important tool for a variety of industries. By monitoring the dew point, it is possible to ensure that gases and liquids are dry enough for safe operation and to prevent condensation.
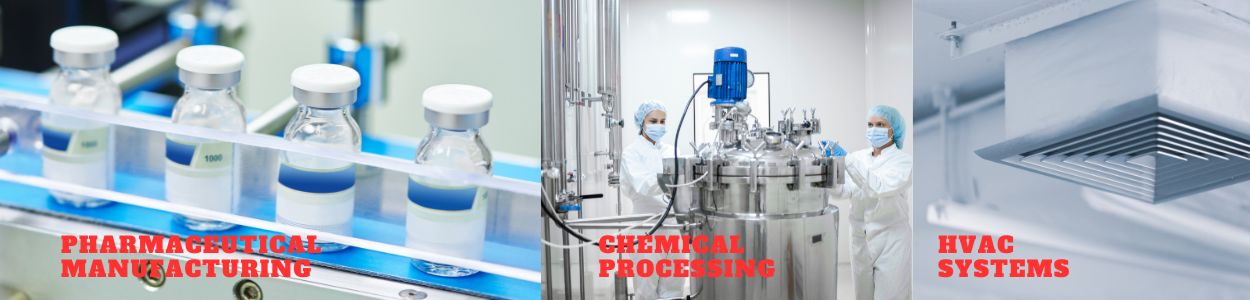
And Here We List Some Clients Whose Industrial Need to Use Dew point sensors and transmitters, please Check it,
Hope it will be help for your Understand More About Application of Dew point sensors and transmitters.
1. Pharmaceutical manufacturing:
Dew point sensors and transmitters are used in pharmaceutical manufacturing to monitor the dew point of air in cleanrooms to ensure that it is dry enough to prevent contamination of products.
2. Food processing:
Dew point sensors and transmitters are used in food processing to monitor the dew point of air in food processing facilities to ensure that it is dry enough to prevent spoilage of food products.
3. Microelectronics:
Dew point sensors and transmitters are used in microelectronics to monitor the dew point of air in cleanrooms to ensure that it is dry enough to prevent contamination of semiconductor wafers.
4. Chemical processing:
Dew point sensors and transmitters are used in chemical processing to monitor the dew point of gases and liquids in chemical processing plants to ensure that they are dry enough to prevent explosions and fires.
5. Oil and gas:
Dew point sensors and transmitters are used in oil and gas production to monitor the dew point of natural gas and other hydrocarbons to ensure that they are dry enough to prevent corrosion of pipelines and other equipment.
6. Power generation:
Dew point sensors and transmitters are used in power generation to monitor the dew point of water in steam turbines to ensure that it is dry enough to prevent turbine damage.
7. Water treatment:
Dew point sensors and transmitters are used in water treatment to monitor the dew point of water in water treatment plants to ensure that it is dry enough to prevent bacteria growth.
8. Air conditioning and refrigeration:
Dew point sensors and transmitters are used in air conditioning and refrigeration systems to monitor the dew point of air to ensure that it is dry enough to prevent condensation and mold growth.
9. HVAC systems:
Dew point sensors and transmitters are used in HVAC systems to monitor the dew point of air to ensure that it is dry enough to prevent condensation and mold growth.
10. Agriculture:
Dew point sensors and transmitters are used in agriculture to monitor the dew point of air to ensure that it is dry enough to prevent crop damage.
Dew point sensors and transmitters are an important tool for a variety of industries.
By monitoring the dew point, it is possible to ensure that gases and liquids are dry enough for safe operation and to prevent condensation.
Videos
Sofeware
T&H Logger Tools
-
Powerful desktop software for displaying measurement data in real-time. No internet connection is required.
Simple, intuitive user interface
It can be realized through RS485 to USB
Smart Logger
Used to realize the recording function: select the timing start as the start mode under the record category of the test software, set the start time and sampling interval, and click Set and Read
Download data: You need to close the test software and then open the Smartlogger software, click the download button (if there is no response) to close the download, and try to click File to download data
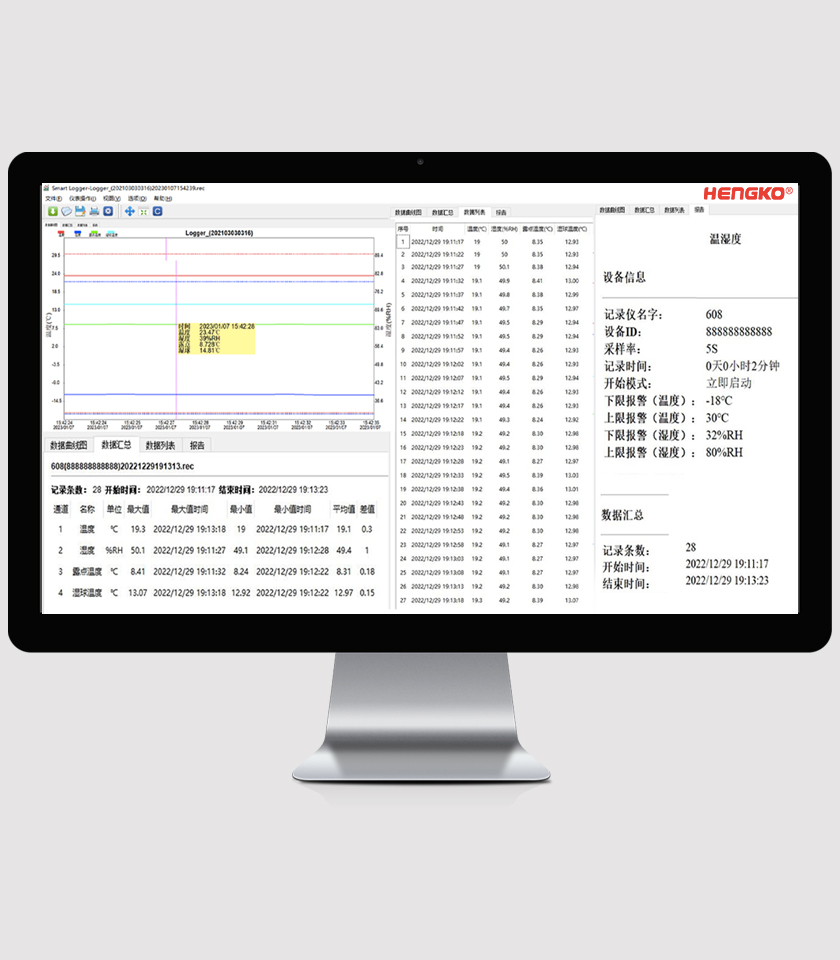
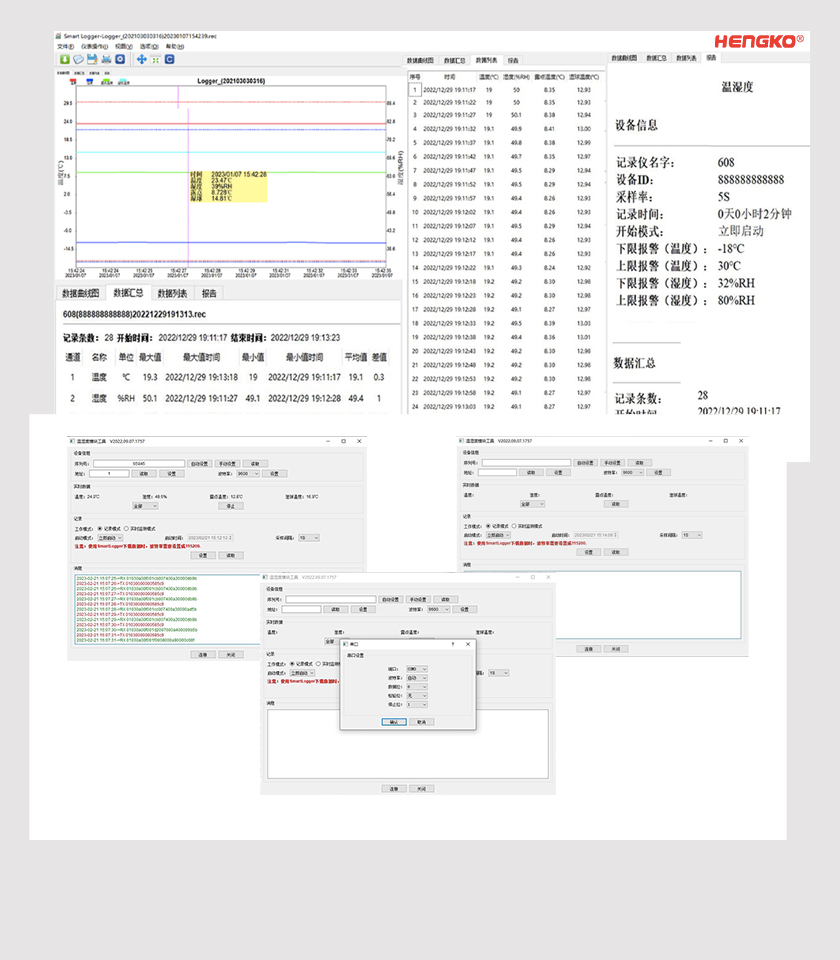
F.A.Q.
The dew point is the temperature at which the unsaturated air lowers its temperature while keeping the partial pressure of water vapor constant (that is, keeping the absolute water content constant) so that it reaches saturation. When the temperature drops to the dew point, condensed water droplets will be precipitated in the humid air. The dew point of humid air is not only related to temperature, but also related to the amount of moisture in the humid air. The dew point is high with high water content, and the dew point is low with low water content. At a certain humid air temperature, the higher the dew point temperature, the greater the partial pressure of water vapor in the humid air, and the greater the water vapor content in the humid air.
Measuring dew point in industrial settings is critical to ensuring that sensitive equipment does not undergo corrosive damage and the quality of end products is preserved.
Measuring the dew point is essential in various applications because it provides crucial information about the moisture content in the air and helps us understand and control humidity levels. The dew point is the temperature at which air becomes saturated with water vapor, leading to the formation of dew or condensation.
Here are some reasons why measuring the dew point is important:
-
Condensation Prediction: By knowing the dew point, we can predict when condensation will occur on surfaces. Condensation can lead to the formation of water droplets, which can cause issues like mold growth, corrosion, and damage to sensitive equipment.
-
Humidity Control: Understanding the dew point allows us to control indoor humidity levels effectively. Maintaining appropriate humidity levels is crucial for human comfort, as excessively high or low humidity can lead to discomfort, health problems, and damage to building materials.
-
Weather Forecasting: Dew point is a key parameter in weather forecasting. It helps meteorologists understand the amount of moisture in the air, which is crucial for predicting the likelihood of precipitation and the formation of fog.
-
Industrial Processes: In various industrial processes, controlling humidity is essential for quality control and optimal performance. Measuring the dew point enables engineers to ensure that the conditions remain within the desired range for efficient production and product quality.
-
HVAC Systems: Heating, ventilation, and air conditioning (HVAC) systems use dew point measurements to determine the appropriate amount of cooling or dehumidification needed to maintain comfortable indoor conditions.
-
Energy Efficiency: Knowing the dew point can help optimize energy consumption in cooling systems by preventing overcooling and unnecessary energy usage.
-
Environmental Monitoring: In environmental monitoring and research, measuring the dew point is crucial for understanding the water vapor content in the atmosphere and its impact on weather patterns, ecosystems, and climate change.
Overall, measuring the dew point provides valuable insights into moisture levels, which impacts various aspects of daily life, industrial processes, and environmental conditions. By monitoring the dew point, we can take appropriate measures to ensure human comfort, prevent damage to materials and equipment, optimize processes, and make informed decisions based on weather patterns.
The terms "dew point" and "pressure dew point" are related to moisture content in the air, but they refer to slightly different concepts. Let's explore the differences between them:
- Dew Point: The dew point is the temperature at which air becomes saturated with water vapor, causing condensation to occur. When the air temperature drops to the dew point, the air is holding the maximum amount of moisture it can at that specific temperature, and any further cooling will lead to the formation of dew, fog, or frost. The dew point is commonly expressed in degrees Celsius (°C) or Fahrenheit (°F).
In everyday terms, the dew point represents the temperature at which dew forms on surfaces, like grass in the morning or windows on a cold night. It is a crucial parameter for understanding and controlling humidity levels, as it indicates the moisture saturation level of the air.
- Pressure Dew Point: The pressure dew point is a concept related to compressed air systems, which are used in various industrial applications. Compressed air systems involve compressing air to higher pressures, which leads to an increase in air temperature. However, the moisture content in the air remains constant, which means the relative humidity decreases as the air is compressed.
The pressure dew point is the temperature at which the moisture in compressed air will start to condense into liquid water under a specific pressure. It is a critical parameter in compressed air systems, as condensation can lead to equipment damage, corrosion, and compromised product quality in industrial processes that use compressed air.
In summary, the main difference between "dew point" and "pressure dew point" is their context and applications. The dew point refers to the temperature at which air becomes saturated with moisture, leading to the formation of dew or condensation in regular atmospheric conditions. On the other hand, the pressure dew point is specific to compressed air systems and represents the temperature at which moisture will condense in compressed air at a given pressure. Both concepts are important for understanding and managing moisture levels in different settings.
Under the condition of constant temperature and confined space, the dew point increases with the increase of pressure, and the dew point decreases with the decrease of pressure (up to atmospheric pressure), which is the influence of dew point and pressure.
Since all dew point meter moisture measurements are derived from the measurement of water vapor pressure, the measurement of the total gas pressure of the system will have an impact on the measured humidity.
Knowing the dew point of compressed air is crucial for several reasons in industrial and commercial applications that utilize compressed air systems. Here are some of the key reasons why it is important to monitor and control the dew point of compressed air:
-
Preventing Equipment Damage: If the compressed air contains moisture, it can condense and form liquid water when the air cools down. This can lead to water accumulation in the compressed air system and cause damage to equipment, such as air compressors, pneumatic tools, and control valves. Water in the system can lead to corrosion, reduced efficiency, and premature wear and tear of components.
-
Protecting Product Quality: In industries where compressed air comes into direct contact with products (e.g., food and beverage, pharmaceuticals), moisture in the air can contaminate the products. Maintaining a low dew point ensures that the compressed air remains dry and clean, safeguarding the quality and integrity of the final products.
-
Avoiding Production Issues: Moisture in compressed air can cause problems in manufacturing processes, such as improper coating, paint defects, and compromised adhesion in surface treatments. Maintaining a low dew point helps to avoid these production issues and ensures consistent and high-quality manufacturing outputs.
-
Reducing Downtime: Condensation in the compressed air system can lead to blockages in pipes, filters, and pneumatic components. This can result in system malfunctions and unplanned downtime for maintenance and repairs. Monitoring the dew point allows proactive measures to be taken, reducing the likelihood of downtime and production interruptions.
-
Enhancing Energy Efficiency: Dry air requires less energy to compress compared to moist air. By maintaining a low dew point, the compressor system operates more efficiently, reducing energy consumption and operating costs.
-
Extending Equipment Life: Minimizing moisture in the compressed air system helps extend the lifespan of equipment and components. Dry air reduces the risk of corrosion and degradation, resulting in longer-lasting and more reliable equipment.
-
Complying with Industry Standards: Many industries have specific quality standards and regulations related to compressed air quality, including dew point requirements. Ensuring compliance with these standards is essential for product safety and regulatory adherence.
In conclusion, knowing and controlling the dew point of compressed air is critical for maintaining the efficiency, reliability, and quality of compressed air systems. By keeping the dew point low, industries can prevent equipment damage, protect product quality, avoid production issues, reduce downtime, improve energy efficiency, and comply with industry standards and regulations.
When measuring the dew point of compressed air with a dew point meter, there are several important factors and considerations that should be taken into account to ensure accurate and reliable measurements. Here are the key points to pay attention to:
-
Calibration: Ensure that the dew point meter is calibrated regularly according to the manufacturer's guidelines or industry standards. Regular calibration is essential to maintain the accuracy of the measurements.
-
Sampling Point: Select an appropriate sampling point to measure the compressed air. Ideally, the sampling point should be located downstream of any drying or filtration equipment to capture the actual dew point of the compressed air being used.
-
Cleanliness: Make sure the sampling point and any connecting tubing are clean and free from contaminants. Any dirt or oil in the sampling system can affect the accuracy of the readings.
-
Pressure and Flow: Consider the pressure and flow rate of the compressed air during measurements. Some dew point meters may require specific pressure and flow conditions for accurate readings.
-
Response Time: Check the response time of the dew point meter. Rapid response times are important in dynamic systems, as they can help capture changes in the dew point quickly.
-
Operating Range: Ensure that the dew point meter is suitable for the expected dew point range of the compressed air. Different dew point meters have different operating ranges, and using a meter beyond its range may result in inaccurate readings.
-
Sensor Type: Be aware of the sensor technology used in the dew point meter. Different sensor types, such as chilled mirror, capacitance, or infrared, have their specific advantages and limitations. Choose a sensor suitable for the application and the required accuracy.
-
Ambient Temperature: The ambient temperature can affect the dew point measurement. Ensure that the dew point meter compensates for variations in ambient temperature, especially if the measurements are taken in different environments.
-
Data Logging and Recording: If necessary, use a dew point meter that allows data logging and recording of measurements. This feature is useful for trend analysis and quality control purposes.
-
Maintenance: Regularly maintain and clean the dew point meter to ensure its optimal performance. Follow the manufacturer's guidelines for maintenance and storage.
By paying attention to these factors and taking proper precautions, you can ensure that the dew point measurements of compressed air with a dew point meter are accurate, consistent, and useful for maintaining the efficiency and quality of compressed air systems.
Use a dew point meter to measure the pressure dew point of compressed air. The sampling point should be placed in the exhaust pipe of the dryer, and the sample gas should not contain liquid water droplets. There are errors in the dew points measured at other sampling points.
Compressed air drying is essential to remove moisture from the air to prevent damage to equipment, ensure product quality, and improve the overall efficiency of compressed air systems. There are several methods used for compressed air drying, each suited to specific applications and dew point requirements. Here are the common compressed air drying methods:
-
Refrigeration Drying: Refrigeration drying is one of the most common and economical methods for compressed air drying. This process involves cooling the compressed air to a temperature where the water vapor condenses into liquid form. The condensed moisture is then separated from the air using a separator or drain trap. The cooled and dried air is then reheated to reach the desired dew point before it enters the distribution system.
-
Desiccant Drying: Desiccant drying employs the use of a porous material called a desiccant, which has a high affinity for moisture. The compressed air passes through the desiccant bed, where the moisture is adsorbed by the desiccant particles. This method is effective in achieving very low dew points, making it suitable for applications requiring extremely dry air, such as in critical industrial processes and sensitive instruments.
Desiccant dryers can be further classified into two types: a. Heatless Desiccant Dryers: They regenerate the desiccant using a portion of the dry compressed air, and the dried air switches between two towers filled with desiccant. b. Heated Desiccant Dryers: These dryers use external heat sources like electric heaters or heat from the compressed air system to regenerate the desiccant, allowing continuous operation.
-
Membrane Drying: Membrane dryers use semi-permeable membranes to remove water vapor from the compressed air. The membranes allow water molecules to pass through, while the dry air remains on the other side. This method is suitable for achieving moderate dew points and is often used for small-scale applications or when a low-maintenance solution is required.
-
Deliquescent Drying: Deliquescent drying involves the use of a hygroscopic substance, such as salt, which absorbs moisture from the compressed air. As the substance absorbs water, it dissolves and forms a liquid solution that is collected and drained. Deliquescent drying is often used in portable or temporary applications and is relatively simple and cost-effective.
-
Membrane + Refrigeration Hybrid Drying: Some advanced compressed air drying systems use a combination of membrane drying and refrigeration drying. This hybrid approach allows for greater energy efficiency and cost savings, as the initial moisture removal occurs with the membrane before the compressed air is further dried using refrigeration.
The choice of compressed air drying method depends on factors like the required dew point, flow rate, energy efficiency, space constraints, and the specific application's needs. It's essential to properly select and maintain the appropriate drying method to ensure the quality and reliability of the compressed air supply.
The compressed air discharged from the air compressor contains many impurities: ①Water, including water mist, water vapor, condensed water; ②Oil, including oil stains, oil vapor; ③Various solid substances, such as rust mud, metal powder, rubber Fines, tar particles, filter materials, fines of sealing materials, etc., in addition to a variety of harmful chemical odor substances.
The compressed air output from the air compressor contains a lot of harmful impurities, the main impurities are solid particles, moisture, and oil in the air.
Vaporized lubricating oil will form an organic acid to corrode equipment, deteriorate rubber, plastic, and sealing materials, block small holes, cause valves to malfunction, and polluting products.
The saturated moisture in the compressed air will condense into water under certain conditions and accumulate in some parts of the system. These moistures have a rusting effect on components and pipelines, causing moving parts to be stuck or worn, causing pneumatic components to malfunction and air leakage; in cold regions, moisture freezing will cause pipelines to freeze or crack.
Impurities such as dust in the compressed air will wear the relative moving surfaces in the cylinder, air motor and air reversing valve, reducing the service life of the system.
Storage: Easily store large volumes of compressed air as needed.
Simple Design and Control: Acting pneumatic components are of simple design and are therefore suitable for simpler controlled automatic systems.
Choice of motion: Pneumatic components are easy to realize linear and rotary motion with stepless speed regulation.
Compressed air generation system, because the price of pneumatic components is reasonable, the cost of the whole device is low, and the life of pneumatic components is long, so the maintenance cost is low.
Reliability: Pneumatic components have a long working life, so the system has high reliability.
Harsh environment adaptability: Compressed air is not affected by high temperature, dust and corrosion to a large extent, which is beyond the reach of other systems.
Clean environment: The pneumatic components are clean, and there is a special exhaust air treatment method, which has less pollution to the environment.
Safety: It will not cause fire in dangerous places, and if the system is overloaded, the actuator will only stop or slip.
A dew point sensor is a device that measures the dew point of a gas. The dew point is the temperature at which water vapor in the gas will condense into liquid water. Dew point sensors are used in a variety of applications, including:
- Compressed air drying: Dew point sensors are used to monitor the dew point of compressed air to ensure that it is dry enough for use in critical applications.
- Refrigeration: Dew point sensors are used to monitor the dew point of refrigerants to ensure that they are dry enough for use in refrigeration systems.
- Humidity control: Dew point sensors are used to monitor the dew point of air to control humidity levels in a variety of applications, such as food processing and pharmaceutical manufacturing.
A dew point transmitter is a device that measures the dew point of a gas and transmits the measurement to a remote location. Dew point transmitters are used in a variety of applications, including:
- Building automation: Dew point transmitters are used in building automation systems to monitor the dew point of air in buildings to control humidity levels and prevent condensation.
- Process control: Dew point transmitters are used in process control systems to monitor the dew point of gases in industrial processes to ensure that they are dry enough for safe operation.
- Environmental monitoring: Dew point transmitters are used in environmental monitoring applications to monitor the dew point of air to track changes in humidity and identify potential problems, such as mold growth.
The main difference between a dew point sensor and a dew point transmitter is that a dew point transmitter transmits the measurement to a remote location, while a dew point sensor does not. This makes dew point transmitters more versatile and useful in applications where the measurement needs to be accessed remotely, such as in building automation and process control systems.
Here is a table that summarizes the key differences between dew point sensors and dew point transmitters:
Feature | Dew Point Sensor | Dew Point Transmitter |
---|---|---|
Measures | Dew point of a gas | Dew point of a gas and transmits the measurement to a remote location |
Uses | Compressed air drying, refrigeration, humidity control | Building automation, process control, environmental monitoring |
Versatility | Less versatile | More versatile |
Cost | Less expensive | More expensive |
You May Also Like
Handheld Humidity Meter
-20~60℃
Easy-to-use handheld humidity meters are intended for spot-checking and calibration.