Filtration is a physical process that separates suspended solids from fluids (liquids or gases) by passing the mixture through a porous medium (filter) that traps the solids and allows the fluid to pass through. Filtration is a crucial step in various industries and applications, including water purification, air pollution control, chemical processing, and pharmaceutical manufacturing.
The choice of filter material is critical for effective filtration and depends on several factors, including:
1. Particle Size:
The size of the particles to be removed is a primary consideration. The filter pore size should be smaller than the particles to be captured but large enough to allow the fluid to flow through at a reasonable rate.
2. Particle Concentration:
The concentration of particles in the fluid also influences the filter material selection. High particle concentrations may require thicker filters or filters with a larger surface area to prevent clogging.
3. Fluid Properties:
The properties of the fluid, such as viscosity, temperature, and chemical compatibility with the filter material, should be considered to ensure efficient filtration and prevent potential damage to the filter.
4. Application Requirements:
The specific application requirements, such as desired flow rate, pressure drop, and purity level, dictate the choice of filter material and configuration.
Common filter materials include:
1. Paper Filters:
Paper filters are widely used for removing coarse particles from liquids and gases. They are inexpensive and disposable but have limited particle size separation capabilities.
2. Membrane Filters:
Membrane filters are made from synthetic polymers or cellulosic materials and offer finer particle size separation compared to paper filters. They are available in various pore sizes and configurations.
3. Depth Filters:
Depth filters consist of a porous matrix of fibers or particles, providing a larger surface area for trapping particles. They are effective for removing fine particles and can handle higher particle concentrations.
4. Activated Carbon Filters:
Activated carbon filters utilize activated carbon, a highly porous material with a large surface area, to adsorb impurities and contaminants from liquids and gases. They are commonly used for water purification and air pollution control.
5. Ceramic Filters:
Ceramic filters are made from sintered ceramic materials and offer high resistance to chemicals and heat. They are often used in high-temperature and corrosive environments.
6. Metal Filters:
Metal filters are constructed from various metals, such as stainless steel, aluminum, or brass, and provide excellent durability and mechanical strength. They are used in applications requiring high precision and filtration efficiency.
Selecting the appropriate filter material is crucial for optimizing filtration performance and achieving the desired separation objectives. Careful consideration of particle size, particle concentration, fluid properties, application requirements, and cost factors is essential when making the right choice.
Sintered Metal Filters
Sintered metal filters are porous structures made from metal powders that are compacted and heated to a temperature below their melting point, causing them to fuse together without melting completely. This process, known as sintering, results in a strong, rigid, and porous filter element with a uniform pore size distribution.
* Manufacturing Process:
1. Powder Preparation: Metal powders are carefully selected and blended to achieve the desired composition and properties.
2. Compaction: The blended metal powders are pressed into the desired shape, often using a mold or die.
3. Sintering: The compacted powder is heated to a temperature below the melting point, causing the particles to bond together, forming a porous structure.
4. Finishing: The sintered filter element may undergo additional processing, such as sizing, cleaning, and surface treatment, to achieve the desired specifications.
* Key properties and characteristics:
1. High Strength:
Sintered metal filters are known for their exceptional strength and durability, making them suitable for high-pressure applications.
2. High Temperature Resistance:
They can withstand high temperatures without compromising their structure or performance, making them ideal for extreme environments.
3. Corrosion Resistance:
Many sintered metal filters are made from corrosion-resistant materials, such as stainless steel, making them suitable for use in corrosive environments.
4. Uniform Pore Size Distribution:
The sintering process ensures a uniform pore size distribution, providing consistent filtration performance and reliable separation of particles.
5. High Flow Rate:
The open pore structure allows for high flow rates of fluids, making sintered metal filters efficient for large-scale filtration applications.
* Applications of Sintered Metal Filters Industrial applications.
Advantages in specific scenarios.
Sintered metal filters are widely used in various industrial applications
due to their unique properties and versatility. Here are some examples:
1. Chemical Processing:
In chemical processing plants, sintered metal filters are used to remove impurities from gases and liquids, ensuring product purity and process efficiency.
2. Pharmaceutical Manufacturing:
They are employed in pharmaceutical manufacturing to purify and sterilize medications, ensuring compliance with strict quality standards.
3. Power Generation:
In power generation systems, sintered metal filters are used to remove contaminants from water and fuel, protecting equipment and enhancing performance.
4. Aerospace and Automotive Industries:
They are used in aerospace and automotive applications to filter lubricants, coolants, and gases, contributing to system reliability and longevity.
Advantages in specific scenarios:
1. High-Pressure Applications:
Sintered metal filters can withstand high pressures without compromising their integrity,
making them ideal for applications such as hydraulic systems and high-pressure gas filtration.
2. Corrosive Environments:
Their corrosion resistance makes them suitable for use in harsh
environments where exposure to chemicals or fluids is a concern.
3. Extreme Temperatures:
Sintered metal filters can maintain their performance under extreme temperatures, making them
valuable in applications such as gas turbine filtration and molten metal filtration.
4. Fine Particle Separation:
Their uniform pore size distribution allows for effective separation of fine particles, making them
suitable for applications such as pharmaceutical filtration and semiconductor production.
5. Biocompatibility:
Certain sintered metal filters are biocompatible, making them suitable for medical applications
such as blood filtration and dental implants.
Sintered Ceramic Filters
Ceramic filters are porous structures made from ceramic materials that are shaped and fired at high temperatures, resulting in a hard, chemically inert, and porous filter element. The manufacturing process of ceramic filters typically involves the following steps:
1.Slurry Preparation: Ceramic powders are mixed with water and additives to form a slurry.
3. Drying: The cast filters are dried to remove excess water and moisture.
4. Firing: The dried filters are fired at high temperatures (typically around 1000-1400 °C) to cause the ceramic particles to sinter and fuse together, forming a dense, porous structure.
5. Finishing: The fired filters may undergo additional processing, such as sizing, cleaning, and surface treatment, to achieve the desired specifications.
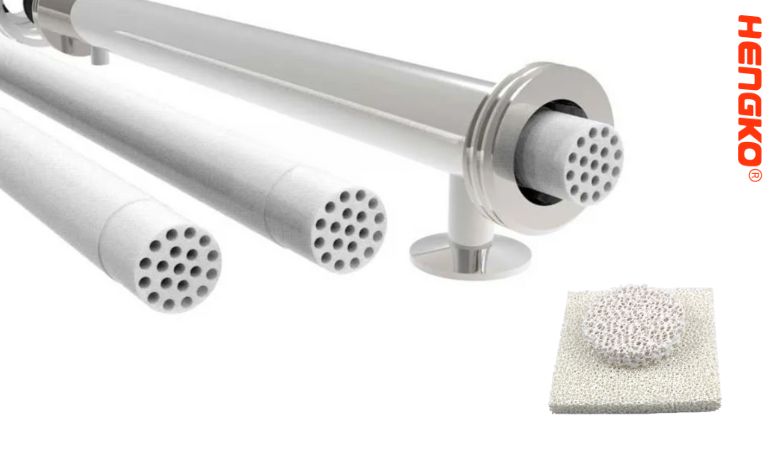
Key properties and characteristics:
* High Chemical Resistance: Ceramic filters are highly resistant to a wide range of chemicals, making them suitable for use in environments with harsh chemical conditions.
* High Temperature Resistance: They can withstand high temperatures without compromising their structure or performance, making them ideal for extreme environments.
* Biocompatibility: Many ceramic filters are biocompatible, making them suitable for medical applications such as water purification and blood filtration.
* Uniform Pore Size Distribution: The firing process ensures a uniform pore size distribution, providing consistent filtration performance and reliable separation of particles.
* High Flow Rate: The open pore structure allows for high flow rates of fluids, making ceramic filters efficient for large-scale filtration applications.
Applications of Ceramic Filters
Usage in different industries:
Ceramic filters have found widespread applications in various industries due to their unique properties and versatility. Here are some examples:
* Water Purification: In water purification systems, ceramic filters are used to remove impurities, bacteria, and viruses from water, providing clean and safe drinking water.
* Pharmaceutical Manufacturing: In pharmaceutical manufacturing, ceramic filters are used to purify and sterilize medications, ensuring compliance with strict quality standards.
* Electronics Manufacturing: They are used in electronics manufacturing to filter and purify ultrapure water used in semiconductor production.
* Environmental Applications: Ceramic filters are used in environmental applications to remove pollutants and contaminants from wastewater and air emissions.
Unique advantages:
* Low Cost: Ceramic filters are relatively inexpensive to manufacture, making them an economical solution for various filtration applications.
* Long Lifespan: They can withstand long-term use and harsh conditions, providing a durable and cost-effective filtration solution.
* Ease of Maintenance: Ceramic filters are generally easy to clean and maintain, making them a low-maintenance option compared to other filtration technologies.
* Environmental Friendliness: Ceramic filters are made from natural materials and can be recycled, making them an environmentally friendly option.
In summary, ceramic filters offer a combination of desirable properties, including high chemical resistance, high temperature resistance, biocompatibility, uniform pore size distribution, and high flow rate, making them a valuable filtration technology for a wide range of industrial and environmental applications.
Comparison of Sintered Metal Filters and Ceramic Filters
Sintered metal filters and ceramic filters are both porous structures used for filtration in various applications. They share some similarities in terms of their ability to separate particles from fluids, but they also have distinct properties and characteristics that make them suitable for different applications.
Feature | Sintered Metal Filters | Ceramic Filters |
---|---|---|
Durability and lifespan | Generally more durable and have a longer lifespan due to their higher mechanical strength | Moderately durable with a relatively long lifespan if handled carefully |
Filtration efficiency and pore size | Efficient filtration with uniform pore size distribution | Efficient filtration with uniform pore size distribution |
Chemical resistance | Resistant to a wide range of chemicals, but some metals may corrode in specific environments | Highly resistant to a wide range of chemicals |
Thermal resistance | Highly resistant to high temperatures | Highly resistant to high temperatures |
Maintenance and cleaning requirements | Easy to clean and maintain | Easy to clean and maintain |
Pros and Cons
Advantages of sintered metal filters:
- High strength and durability
- High temperature resistance
- Good resistance to mechanical shock and vibration
- Wide range of applications, including high-pressure and high-temperature environments
Disadvantages of sintered metal filters:
- Some metals may corrode in specific environments
- More expensive than ceramic filters
- May not be suitable for filtering very fine particles
Advantages of ceramic filters:
- High chemical resistance
- Biocompatible and suitable for medical applications
- Relatively inexpensive
- Easy to clean and maintain
Disadvantages of ceramic filters:
- More fragile than sintered metal filters
- May not be suitable for very high-pressure applications
How to Selecting the Right Filter for Your Needs
Choosing the right filter for your specific needs requires careful consideration of various factors, including the intended application, the characteristics of the fluid to be filtered, and the desired filtration performance. Here's a step-by-step guide to making an informed decision:
1. Identify the Application and Filtration Objective:
Clearly define the purpose of the filtration process and the specific goals you aim to achieve. Are you removing impurities from water, separating particles from a gas, or purifying a chemical solution?
2. Understand the Fluid Properties:
Analyze the characteristics of the fluid to be filtered, including its viscosity, temperature, chemical composition, and the presence of suspended solids or contaminants.
3. Evaluate Particle Size and Concentration:
Determine the size and concentration of the particles you intend to remove. This will help narrow down the filter options with appropriate pore sizes and effective filtration capabilities.
4. Consider Flow Rate and Pressure Requirements:
Assess the desired flow rate of the filtered fluid and the pressure conditions the filter will encounter. This will ensure the filter can handle the flow demand and withstand the operating pressure.
5. Evaluate Chemical and Thermal Compatibility:
Ensure the filter material is compatible with the chemicals present in the fluid and can withstand the operating temperature range. Select filters that are resistant to corrosion and maintain their integrity under the expected thermal conditions.
6. Cost and Maintenance Considerations:
Factor in the initial cost of the filter, as well as ongoing maintenance and replacement expenses. Balance the performance requirements with the overall cost-effectiveness of the filter option.
7. Seek Expert Guidance:
If you have complex filtration requirements or need assistance in selecting the most suitable filter, consult with experienced filtration professionals or the filter manufacturer. They can provide tailored recommendations based on your specific application and fluid characteristics.
In summary, selecting the right filter involves a comprehensive evaluation of the application, fluid properties, particle characteristics, flow rate requirements, chemical compatibility, thermal resistance, cost considerations, and expert guidance when necessary. By carefully considering these factors, you can make an informed decision that ensures effective filtration, optimal performance, and long-term value.
Sintered metal filters and ceramic filters are two prominent filtration technologies, each offering unique advantages and suitability for different scenarios. Sintered metal filters excel in high-pressure applications, high-temperature environments, and situations where mechanical strength and durability are critical. Ceramic filters, on the other hand, shine in applications demanding high chemical resistance, biocompatibility, and cost-effectiveness.
If you're seeking expert advice or need more information about advanced filtration solutions, HENGKO is here to help. Don't hesitate to reach out to us for tailored guidance and professional insights. Simply send an email to ka@hengko.com and our dedicated team will be delighted to assist you with your specific needs. Whether it's a question about sintered metal or ceramic filters, or a custom requirement, we're just an email away!
Email us now at ka@hengko.com and let's explore the ideal filtration solutions together!
Send your message to us:
Post time: Dec-01-2023